EXTRUSION
EXTRUSION
AMT Plastics has had an incredible journey over the past 30+ years, marked by impressive growth and innovation. Today, we proudly operate a fleet of 20 extrusion machines, a testament to our vast experience and expertise. This journey has equipped us with the skills needed to consistently deliver top-quality parts on time, reinforcing our commitment to excellence and reliability in everything we do.
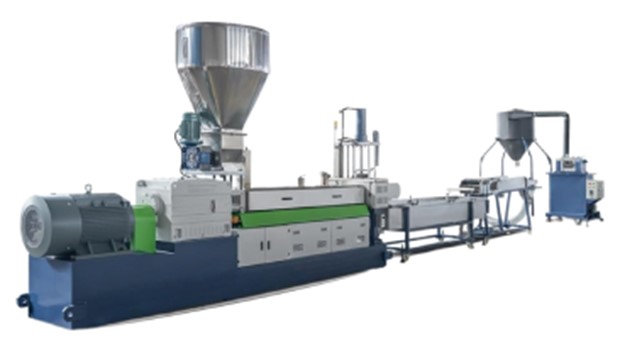
98%
On-time Delivery
23
Extruders
98%
Part Acceptance

Extruder Options
- Vertical, single, and twin screw configurations
- Capable of producing profiles as wide as 14 inches
- Co-extrusion and tri-extrusion capabilities for versatile production

Engineering Solutions
- On-site die design and fabrication
- Metal-to-plastic reverse engineering for optimized conversions
- Comprehensive part evaluation and analysis to ensure precision and performance

Material Selection Expertise
- Comprehensive resin evaluation and selection
- Resin options tailored to specific applications
- Strategic material partnerships to ensure cost-effective solutions
At AMT Plastics, we embrace engineering innovation and flexibility to enhance your product lifecycles and boost cost-effectiveness.
At AMT Plastics, we’re driven by a passion for continuous innovation! By blending engineering expertise, top-notch product performance, and smart cost optimization, we’re dedicated to cutting costs and minimizing waste at every stage of your product’s lifecycle, ensuring maximum efficiency and value.
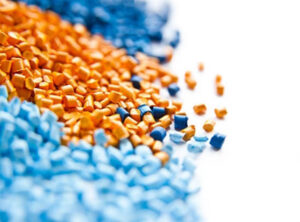
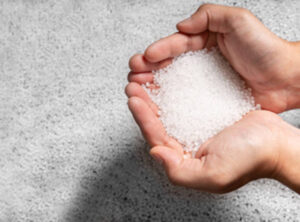
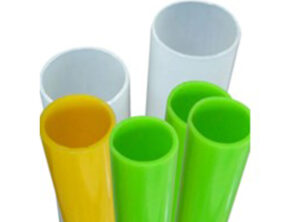
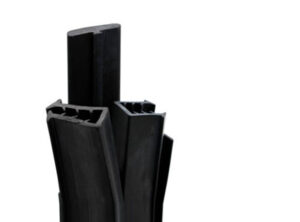
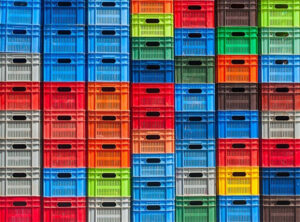

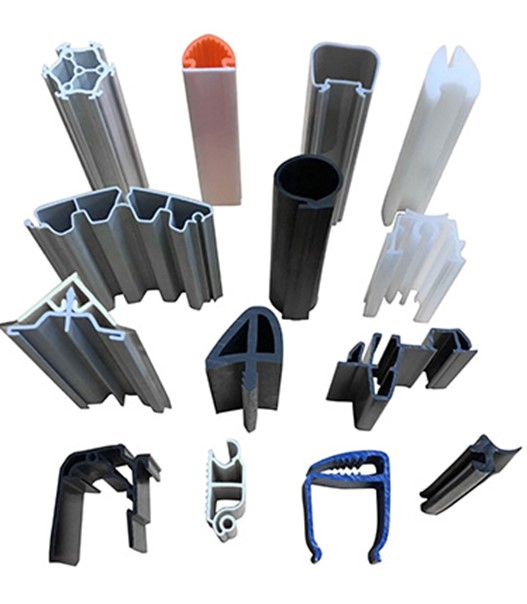
Extruder Options

Profile Extrusion:
Single-screw extrusion utilizes a single rotating screw within a barrel to continuously feed and shape plastic through a metal die, producing profiles with precise dimensions and consistent quality.

Co-Extrusion:
Co-extrusion combines different types of plastic materials in a single process, allowing for extruded parts with enhanced properties such as varied strength, flexibility, or chemical resistance.

Tri-Extrusion:
Similar to co-extrusion, tri-extrusion involves using three different materials to form a single part, offering even more versatility and advanced performance characteristics in the final product.
Engineering Services

Detailed Part Review and Analysis:
We thoroughly assess your part designs, extracting critical insights to develop innovative and effective solutions that enhance product quality and functionality.

Custom Die Design and Fabrication:
Our experts collaborate with you to ensure that your designs meet manufacturing standards and align with your specific project needs, delivering optimized die solutions.

Preventative Maintenance of Equipment and Tools:
We employ a proactive maintenance strategy, ensuring that all machinery and tooling remain in top condition, leading to consistent quality and minimized downtime.
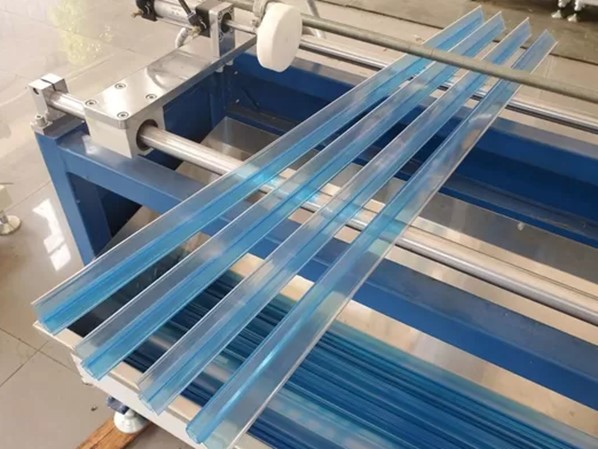
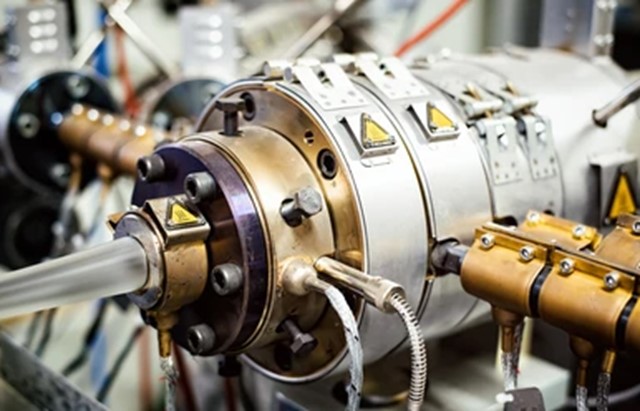
Material Selection Expertise

In-Depth Resin Evaluation and Selection:
Advances in polymer science have introduced a wide variety of resin options. We focus on identifying the best alternatives that are both readily available and cost-efficient to meet your specific project needs.

Plastics Experts Offering Resin Recommendations:
Our team thoroughly assesses factors such as mechanical properties, chemical resistance, environmental conditions, performance, and material shrinkage. Based on this detailed evaluation, we recommend the most suitable resin options for your project.

Strategic Resin Partnerships:
We maintain long-standing relationships with leading resin suppliers across the country. With many years of experience, we ensure access to high-quality commodities and specialty resins that meet the highest manufacturing standards.
Materials
Materials We Work With
ABS
Acrylic
Acrylic
LDPE
A glass alternative, Polymethyl Methacrylate has high tensile and flexural strength, UV resistance, and transparency.
A glass alternative, Polymethyl Methacrylate has high tensile and flexural strength, UV resistance, and transparency.
Polyvinyl Chloride is one of the most versatile plastics. It comes in two types—rigid and flexible—and is dense with good tensile strength.
MDPE
PVC
PC
PP
With properties between HDPE and LDPE, MDPE has excellent shock and drop resistance properties. MDPE is less dense than HDPE but stronger than LDPE.
Compared to HDPE, the molecules of LDPE are more branched out, making the thermoplastic weaker but more flexible. LDPE can be translucent or opaque.
Polycarbonates are a group of polymers that contain carbonate groups within their chemical structures. Polycarbonates are used in a wide variety of applications typically where impact resistance and transparency are required.
Polypropylene is a widely used thermoplastic popular for its high melting point and low level of electrical conductivity. On top of this, Polypropylene does not break down easily but is resistant to cracking and stress.
PETG
HIPS
PU/TPU
TPU
Both transparent or colored, Polystyrene provides good elasticity and flexibility. It can be manufactured as a solid or foam.
TPE is a physical mix of polymers . It can be stretched to twice its original length and still return to its original shape. TPE is similar to TPR, but is more soft and flexible.
Polyurethane boasts excellent elasticity and clarity and also provides protection from grease, oil, or other damage.